News
Keep up to date with all the latest News from Adelco.
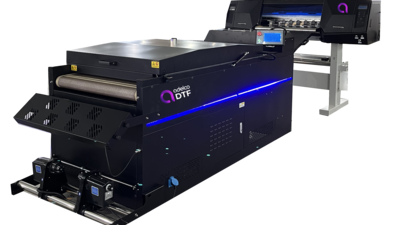
Why Precision Matters: The Role of Accurate Cutting in DTF Printing
In the world of garment printing, precision is everything
Read the article
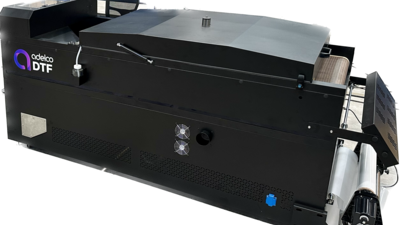
Eco-Friendly Printing: How Integrated DTF Systems Reduce Waste
The printing industry is turning to more eco-friendly methods to reduce waste and minimise environmental impact.
Read the article
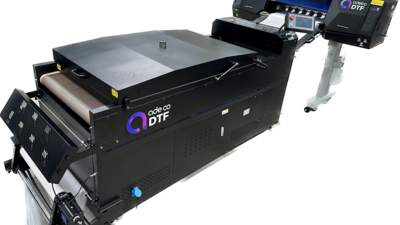
A Beginner’s Guide to DTF Printing and Cutting: What You Need to Know
For anyone stepping into the world of garment printing, Direct-to-Film (DTF) printing offers a versatile and efficient way to create vibrant, durable designs on
Read the article
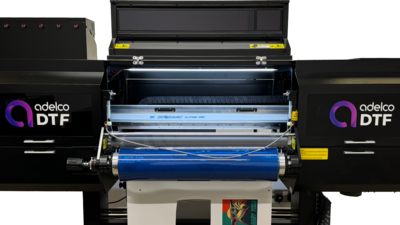
Effortlessly Apply Designs with Adelco’s Versatile UV DTF Printing Technology
Adelco’s UV DTF technology is designed to simplify the process of applying vibrant, long-lasting designs to a wide range of substrates
Read the article
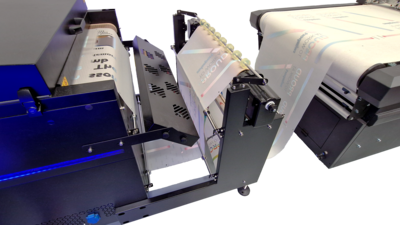
Top 5 Benefits of Combining Printing and Cutting in One DTF System
This article highlights the top five benefits of using an integrated DTF system and how it can transform your production process.
Read the article
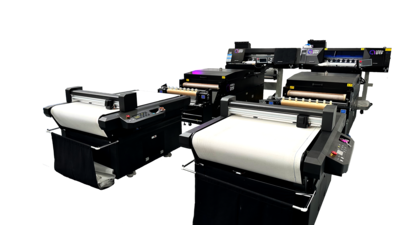
The Ultimate Guide to Integrated Print-and-Cut Systems for DTF Printing
In the ever-evolving world of textile printing, Direct-to-Film (DTF) technology is reshaping the industry with its innovative approach to garment decoration.
Read the article
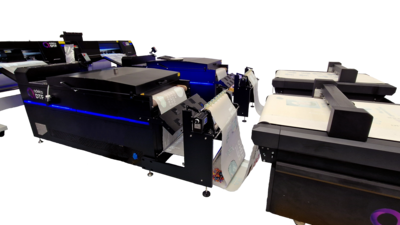
How to Optimise Your Textile Printing Workflow with Integrated DTF Technology
Here’s how you can optimise your textile printing workflow using high-efficiency DTF printing systems.
Read the article
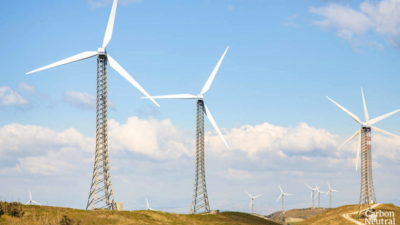
Getting Adelco to Net Zero
Adelco achieves the prestigious status of being a carbon neutral organisation
Read the article
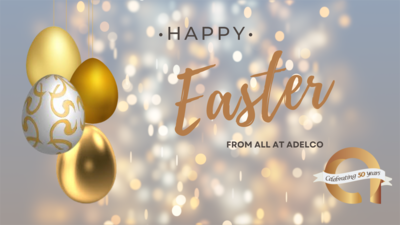
Easter opening hours 2023
Our offices will be closed for the Easter 2023 bank holiday. See our updated opening hours here.
Read the article
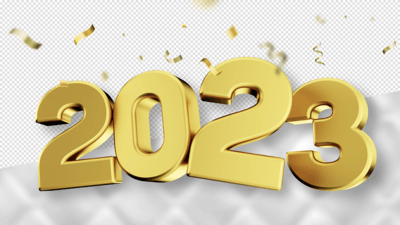
Adelco's New Year's Blog for 2022
Taking a look back at 2022 and towards the future for 2023.
Read the article

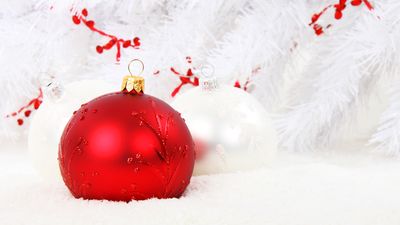
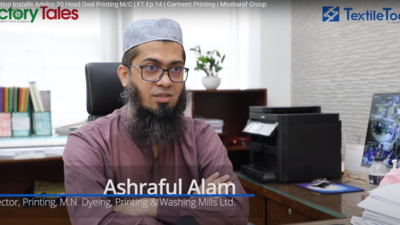
MN Printing installs 2 x 20 Head Adelco Matrix Oval Printing Press.
Bangladesh company Mosharaf Group talk about their new machines.
Read the article

FESPA 22
Adelco revealed new drying solutions at the Global Print Expo this Spring!
Read the article
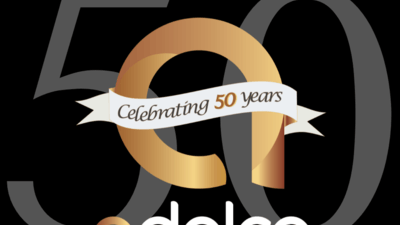
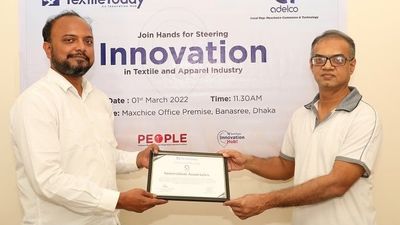
Textile Today Associate
MaxChoice (Adelco Distributors) in Bangladesh become associated with Textile Today.
Read the article
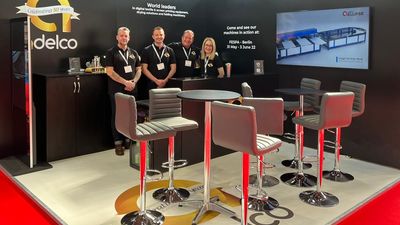
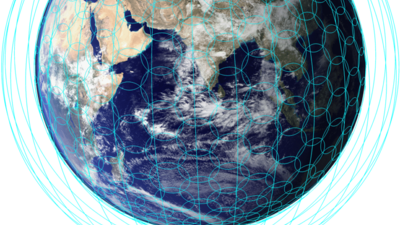
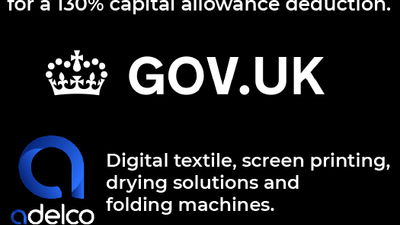
Super-deduction tax relief scheme
The UK Government's new capital allowance deduction.
Read the article
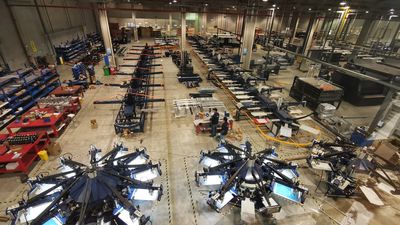
Adelco announce surprising results
2020 will be considered a difficult year for most businesses as a result of the pandemic, but Adelco are one of many that have seen positive results.
Read the article
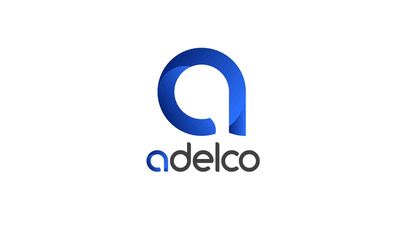
New Logo and Branding
Adelco has undergone a brand transformation after more than forty years using our original logo.
Read the article
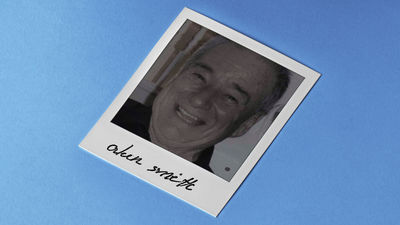
Alan Smith Q & A
Adelco founder, Alan Smith answers questions about Adelco's early days.
Read the article
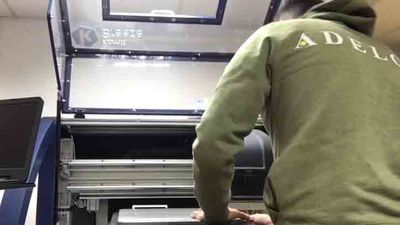
How to safely shut down your DTG machine
Adelco Service Manager, Rob, explains how to safely shut down your digital printer to help ensure excellent DTG print quality.
Read the article
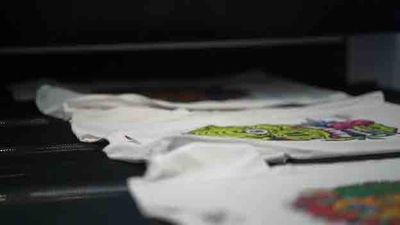
Curing today's textile inks
The importance of curing within the screen-printing process is crucial. This helpful article walks you through all you need to know.
Read the article