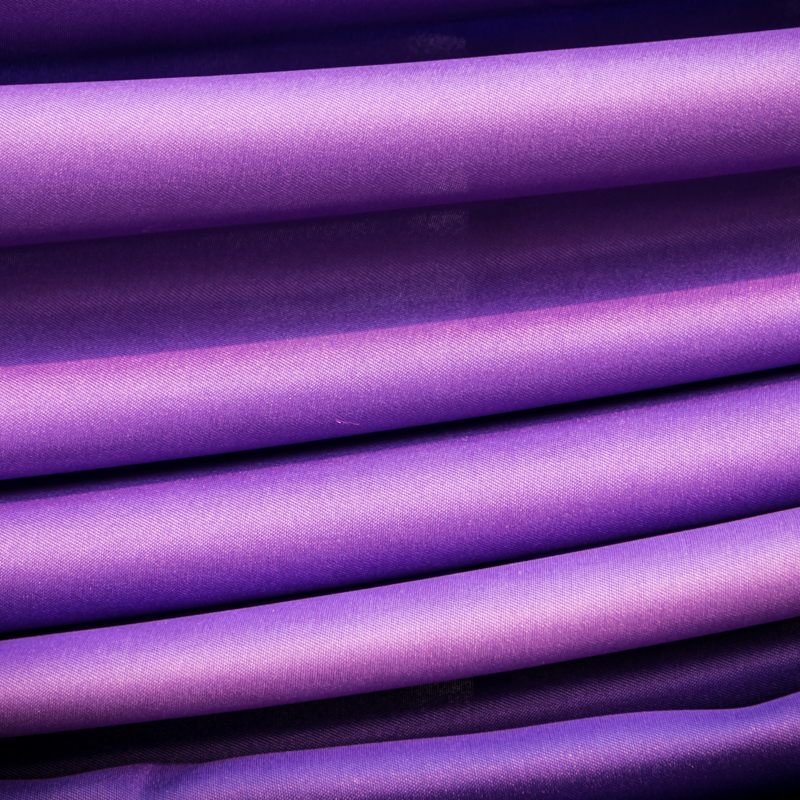
Adelco Digital Printers
Elevating Fabric Printing with High-Speed, Eco-Friendly Digital Printer Solutions
Textile & T-Shirt DTF Printers
Discover Adelco's innovative range of digital printing machines for textiles and fabrics, crafted to bring high production capabilities and efficiency to your business. Our digital printers, designed for a quick setup and eco-friendly operation, are the epitome of modern textile printing solutions.
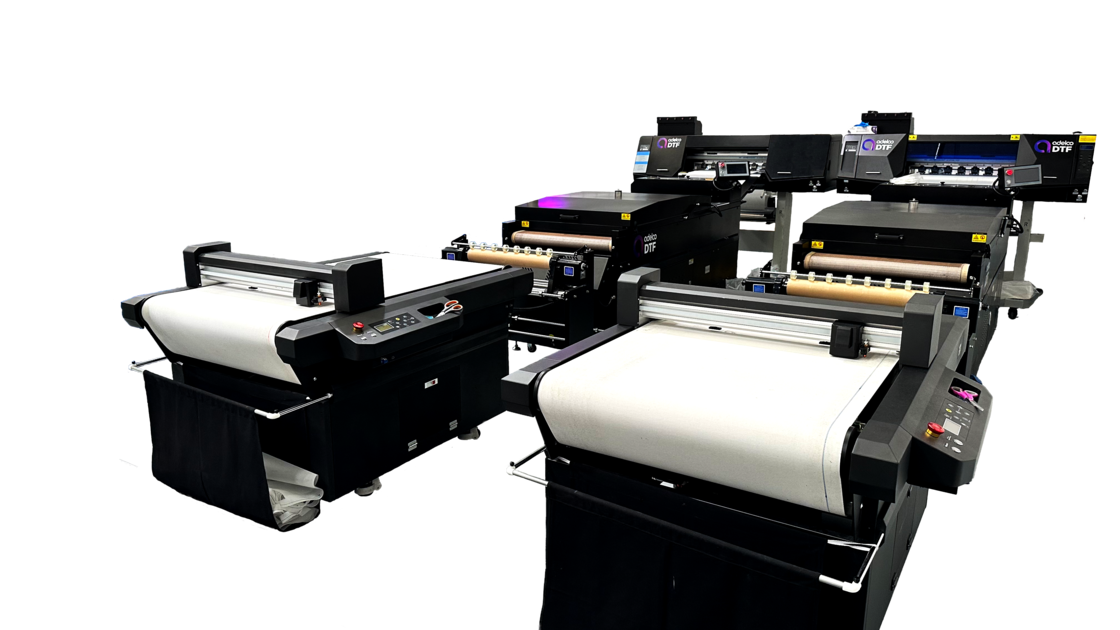
DTF Inline - Integrated Print & Cut Systems
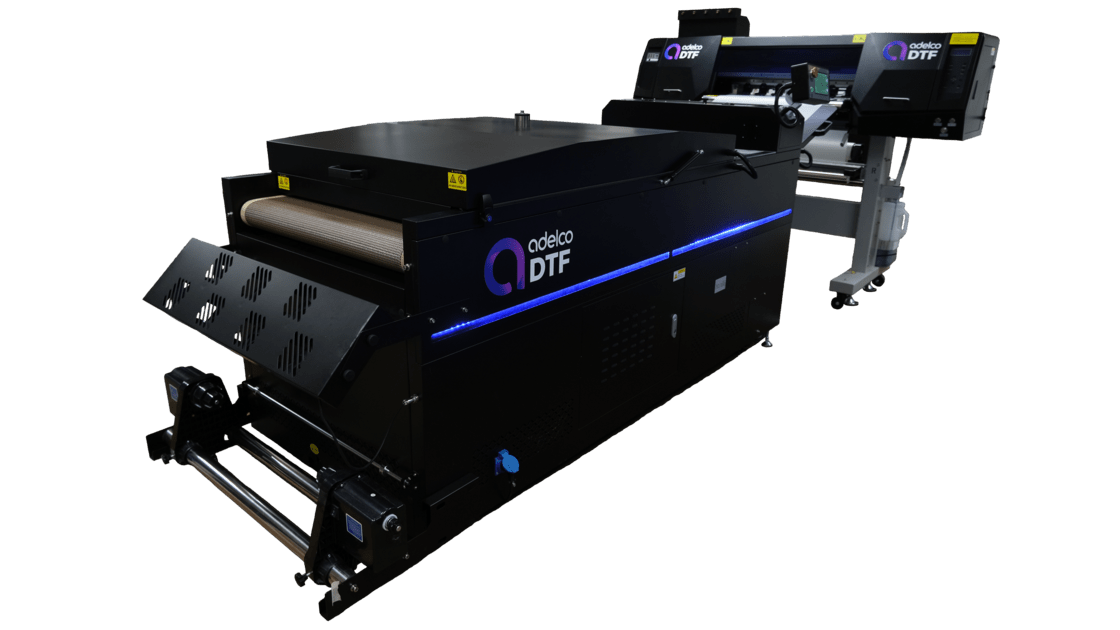
Adelco DTF Printer
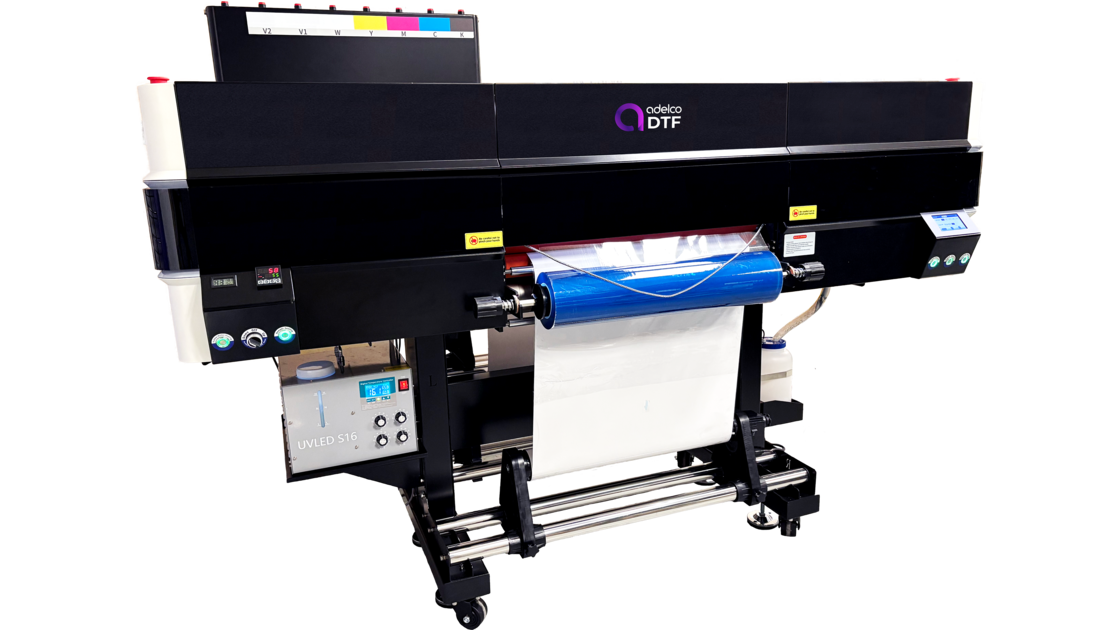
Double-Sided UV DTF
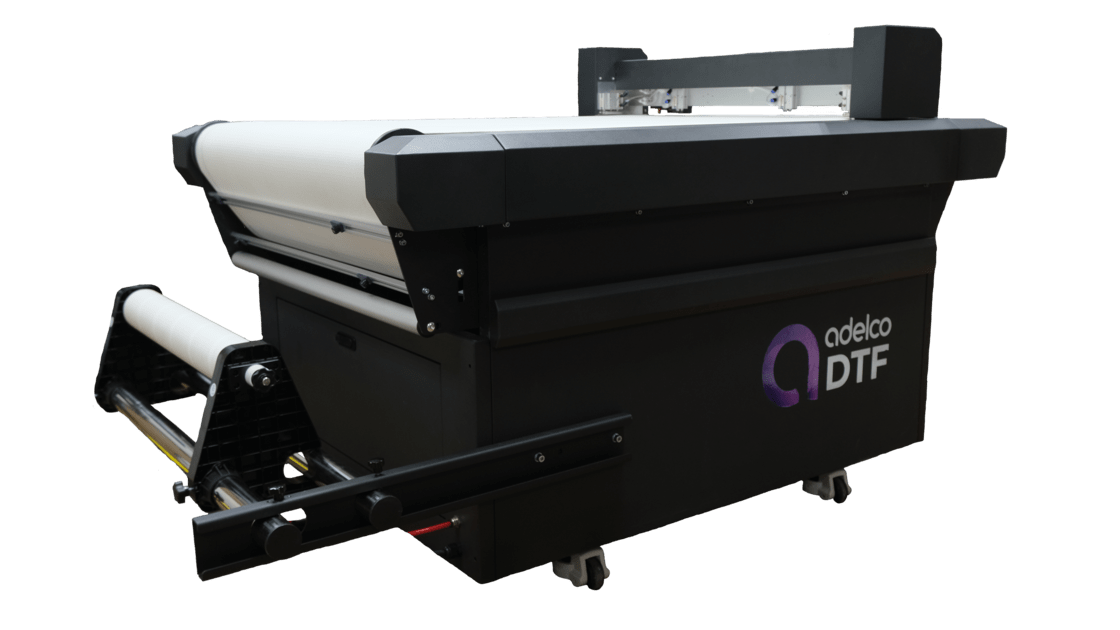
DTF Cutter
Exploring the Advantages of Adelco's Digital Screen Printing Equipment
Time-Saving, Eco-Friendly, and Simplified Printing Processes
Understand how digital printing machines from Adelco bring significant benefits to your t-shirt and textile printing business, including reduced colour-matching time, streamlined processes, and a smaller environmental footprint.
- High Quality: Achieve crisp, detailed prints with exceptional durability.
- Versatile: Suitable for various fabrics, including cotton, silk, and polyester.
- Cost-Effective: Lower printing costs compared to traditional methods, especially for medium to large runs.
Economic and Efficient: The Role of DTF Printers in Textile Printing Solutions
Cost-Effectiveness for Small to Medium Production Runs
Learn why Adelco's DTG printers are more economical than traditional screen printing for smaller production runs, offering quick printing times and fewer setup costs.
Fabrics and Versatility: Adelco's Digital Screen Printing Equipment
Suitability of Various Fabrics for DTF Printing
Explore the range of fabrics compatible with Adelco's high-spec DTF printers, such as the OvalJet, and how they can achieve high-quality prints on materials including cotton, silk, and more.
Choosing the Right Digital Textile Printer: Adelco's Expert Advice
Meeting Your Demands with High-Quality Print Heads and Reliable Support
Consider key factors when selecting a digital textile printer, including demand capacity, print head quality, and customer support. Adelco is here to guide you to the right choice based on your production needs.
FAQs: Understanding Adelco's Digital Textile Printing Solutions
- What is DTF Printing?
-
DTF (Direct to Film) printing involves transferring prints onto a special film which is then applied to textiles, known for its versatility and quality.
- Is DTF Printing Better than Sublimation?
-
DTF printing offers greater fabric compatibility and print durability, making it a preferred choice for many businesses.
- Does DTF Print Last Long?
-
Yes, DTF prints are known for their longevity and resistance to washing and wear.
- What types of fabrics are compatible with Adelco’s digital printers?
-
Adelco's digital printers can handle a variety of fabrics, including cotton, silk, wool, denim, and Lycra. Check out our Matrix Oval for versatile fabric printing options.
- What sets Adelco’s digital printers apart from other printers in the market?
-
Adelco’s digital printers stand out for their high-speed printing capabilities, eco-friendly operation, and ability to print on a wide range of fabrics with precision.
- How do Adelco’s printers contribute to sustainable printing practices?
-
Our printers use eco-friendly, water-based inks and operate with energy efficiency, aligning with our commitment to sustainability. For more on our eco-friendly initiatives, visit our FAQ section.
- Can Adelco’s digital printers integrate with existing screen printing setups?
-
Absolutely. Adelco’s digital printers, like the Adelco Hybrid Digital, are designed to seamlessly integrate with existing screen printing setups, enhancing your printing capabilities.
- Are Adelco’s digital printers suitable for small-scale businesses?
-
Yes, our printers are ideal for businesses of all sizes. They offer cost-effective solutions for small-scale operations, with easy setup and minimal maintenance. Discover more about our printers here.
- How does Adelco ensure the longevity and quality of its digital printers?
-
We use high-quality components and offer comprehensive customer support, including regular maintenance and software updates, to ensure the longevity and peak performance of our printers.
- What training and support does Adelco provide for new digital printer users?
-
Adelco offers extensive training and support for new users, including operational training, technical assistance, and ongoing customer service. Reach out to our support team for more information.
- How cost-effective are Adelco’s digital printers for medium to large print runs?
-
For medium to large print runs, our digital printers like the Adelco DTF Printer offer an economical solution with lower ink costs and faster production times.
- Can I see a demonstration of Adelco’s digital printers before purchasing?
-
Yes, we welcome potential customers to see our printers in action. Contact us to arrange a demonstration.
- Where can I find more information about purchasing an Adelco digital printer?
-
For detailed information about purchasing and financing options, please visit our product page or contact our sales team.